With the loss of my preferred frequent flyer status, airlines tightening their checked luggage allowances, and the addition of another traveler to the family, I’ve been contemplating a new portable antenna that is easier to pack than my usual DK9SQ mast and dipoles. I don’t do high-priced reduced-size antennas if at all possible since portable installations usually have other efficiency-reducing problems. Multi-element antennas take up additional space and have feeding and installation complications that are unnecessary for the casual DX operator. So, that leaves us to choose between a vertical and a dipole.
A few words about efficiency: Dipoles have a distinct efficiency advantage over verticals in almost every practical installation for 40 meters and up, except when the vertical is physically placed in or over salt water. Radiation efficiency tends to be dominated by near-field conditions, pattern is dominated by stuff that’s farther away. This is why vertical dipoles work so well for long-haul DX when placed within a few wavelengths of salt water. They don’t need the near-field efficiency enhancement as much as base-fed verticals, but they still leverage salt water for developing their far-field radiation pattern, especially at low angles required for long-haul communication.
I’m a casual DX operator, not a DXpeditioner, so I never operate on 160 or 80 meters. That is, considering the discussion above, why I have been using dipoles with the DK9SQ. But, verticals have a distinct advantage over dipoles in the sense that they are self-supporting. I decided to build a vertical because: 1) my next DX trip would include time near a beach and 2) I wanted to be able to bring my own support as I had with the DK9SQ.
My remaining requirements were now simple:
- A vertical antenna that requires no additional supports. Guying is OK.
- The antenna must be full-size (quarter wavelength) on 40 meters and above.
- Experience has shown that multi-band operation is desirable, but instant band switching is not necessary.
- The longest piece must fit inside my suitcase (20 in / 50.8 cm maximum length).
- Field assembly and repair with only a Leatherman tool.
- Minimum cost, minimum weight, minimum volume, minimum installation time.
And this is what I came up with:
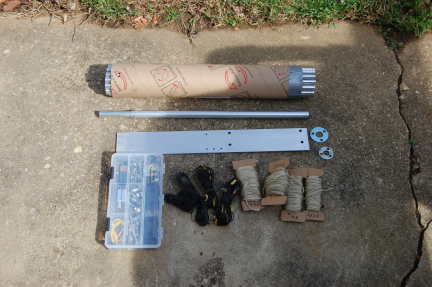
There are 21 aluminum sections, most with a “swaged” (actually, a poor-man’s swage to be described in a moment) end and a slit end. They are shown here bundled perfectly inside a section of cardboard shipping tube. An 18 x 2.5 x 0.125-inch aluminum plate serves as the base. I used DX Engineering resin support blocks to insulate vertical from the base. A point could be fashioned on the bottom of the base and a foot plate attached to push into soft soil, but that has not been done.
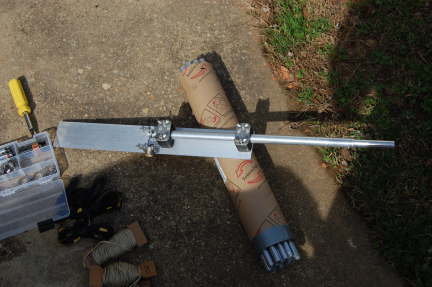
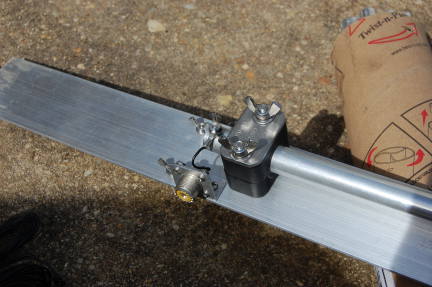
Most sections fit together using overlapping joiner pieces that I previously referred to as “poor-man’s swaging.” I’m not sure that it’s actually a savings over paying a local shop to swage the ends for you when time is considered in addition to material, but I cut telescoping pieces six inches long and fastened them three inches deep in one end of a 17-inch section of tubing with two offset and orthogonally-placed aluminum pop rivets for a total length of 20 inches. This geometry not only fits in my suitcase, but results in a very small amount of wasted material as well.
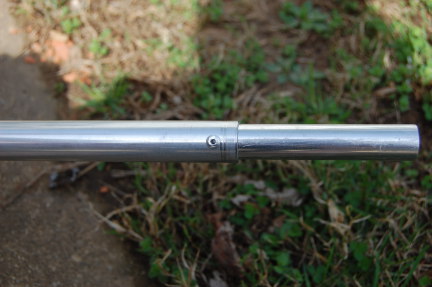
The other end of each piece is slit about 2 inches and they mate with an all-stainless steel hose clamp. The first 10 feet of the antenna are 0.75-inch 6063-T832 tubing followed by telescoping sizes down to 0.375-inch at the very top. The transition pieces are a full 20 inches long and are slit on both ends. The full-size antenna will stand in a light breeze, but guying is a good idea. Guy rings are fashioned out of flat washers drilled in three places.
Tune-up is easy…the more radials you use, the less critical their length. After about 8 or 10, you’re in the clear here. I never attached enough to prevent them from affecting the tuning. If you only plan to have a couple of radials, go ahead and cut them to 1/4 wavelength (even though ground proximity will detune them). Then, set the length of the antenna using the required number of 17-inch sections (the 234/f formula is surprisingly close) with the last section being a variable length for fine tuning.
I’ve intentionally left out most of the details of the antenna itself because I don’t expect anyone duplicate it exactly. But, here are a few notes for anyone considering building one themselves:
- There are lots of parts vendors out there. McMaster-Carr and DX Engineering will get you there in one order from each. There is a surprising amount of overlap in their inventories. Get the hose clamps from McMaster…even if you get stainless-stainless (stainless band, stainless screw), they are about 1/3 of the DXE price. On the other hand, the resin support blocks are cheaper from DXE.
- I carry a compact antenna analyzer (Autek Research VA-1) with me. Field tune-up is a snap and it runs on a single transistor battery. It’s about 1/4 the size and weight of an MFJ-259 and good enough for amateur work. Oh, and I bought mine used for a fraction of the MFJ.
- A tubing cutter is fine if you only have a half-dozen or so cuts. But, if you have a chop saw or need an excuse to buy a chop saw, it will make cutting the tubing far easier. My hands were raw for a few days after cutting the tubing by hand. I’m sure the antenna performs better on account of it, though.
- Find a friend with a metal-cutting bandsaw to slit the ends of your tubes. I went through a half pack (McMaster mega-size pack) of cut-off wheels for my rotary tool doing my slits.
- McMaster only sells the aluminum plate in 36-inch pieces. If you don’t have the aforementioned chop saw, an angle grinder with a cut-off disk does a surprisingly good job.
- I pack a combination-screwdriver that has hex drivers that fit the hose clamps and #6 nuts. Even though the antenna can be erected with only a Leatherman tool doesn’t mean it has to be.
- The small parts box shown in the top picture holds all of the parts for the antenna—it was 2 USD at Home Depot.
- The final and most critical component is a clip-lead that can be used to attach various nearby metal structures to your ground plane. I have used it to make a temporary radial out of excess tubing sections on 12 meters as well.
That’s it. The antenna goes up in a few minutes, especially if not used at full length. I used it successfully last week as OA5/K8GU, which will be detailed in a future post.